Vacuum Deoiling Furnaces
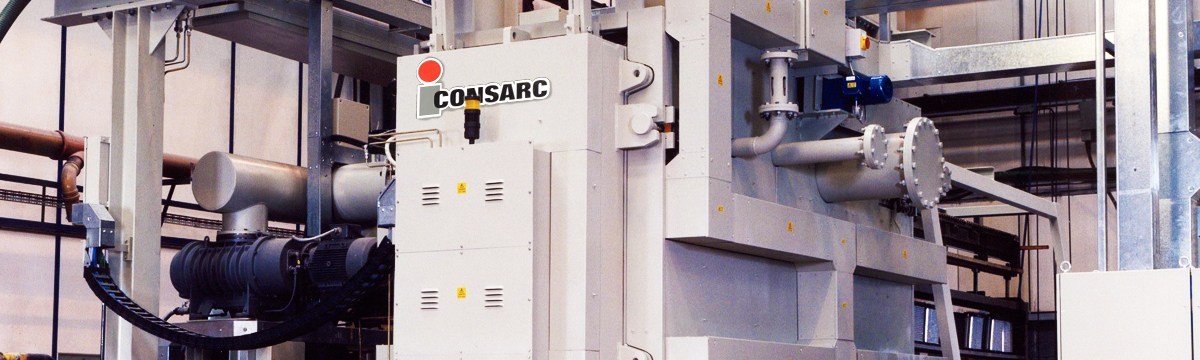
The removal of forming and pressing oils from components prior to further processing, particularly vacuum heat treatment and brazing, is an essential manufacturing step. This was historically achieved using trichlorethane and CFC based solvents. However the phasing out of these ozone depleting and hazardous solvents created a world-wide need for alternative deoiling processes.
Consarc have developed a range of vacuum thermal deoiling furnaces to remove oils by volatilization at low pressure and temperature.
Unlike aqueous cleaning processes, vacuum deoiling does not have any requirements for waste water treatment. Also, oil removed from the components can be recycled.
For removal of the oil, furnaces are fitted with a specially designed vacuum pumping system that produces the vacuum levels required for volatilization of the oils. The vacuum system is also configured to operate within the environment generated as the oil is pumped out of the chamber and discharged at the pump exhaust for collection.
In operation, the internal walls of the vacuum deoiling furnace are maintained in a hot condition to prevent condensation of oil vapors within the furnace.
For the manufacture of vacuum brazed aluminum heat exchangers, vacuum deoiling furnaces can be integrated with new or existing brazing furnaces as a combined production operation.
Features
- Temperature operation to 249oC under vacuum to remove volatile oil contaminants on the surfaces of the component
- Non contact vacuum technique – can remove oils from external and internal surfaces of components by volatilization (oil type dependent). No solvents or aqueous cleaners required. Leaves component clean and dry with no trapped liquids.
- Vacuum and partial pressure operation possible to suit oil characteristics
- Specially designed vacuum pumping system traps all oil at the pump exhaust where it is contained for easy recycling / disposal. No oil / water /solvent mixtures for disposal
- Multiple ‘trimable’ heating panels for balance of heat input to match the workload and fixture thermal characteristics.
- Individual heating elements can be removed without the need for a full hot zone strip down.
- The tank walls of the furnace are maintained in a hot condition to prevent condensation of oils on internal surfaces and ensure complete removal.
- Metallic sheathed elements with external power connection are used to prevent risk of arcing or fire inside process chamber / deoiling environment
- Inert gas backfill with external air blast cooling stations are available
- Fully integrated and automated loading systems.
- Integration with a Vacuum Aluminum furnace to provide an “in line” process system for high productivity with minimum product handling. Also serves as a preheating station to reduce the cycle time in brazing furnace.
- Extensive process experience.
- PLC and PC SCADA providing completely automated control of the brazing furnace and data recording
- Complete furnace system including all interconnecting services, water lines, air lines, gas lines and electrical cables.
- Fully assembled and functionally tested prior to shipment
Tech Specs
Vacuum deoiling systems are custom built to suit individual applications and processes.
Accessories
- Outer Loop Cooling System (Open or Closed)
- Installation Services
- Load tray and carriers
- Manual and automated load handling systems
- Process heating cycle optimisation features
- External air blast cooling systems